Hoje, quando se pensa em impressão 3D, quase sempre o método que vem à mente é o “Fused Deposition Modeling” ou “FDM”. Ou, para ser mais preciso: “Fused Filament Fabrication”, que foi o novo nome que o projeto reprap, responsável pela popularização da Impressão 3D com a queda da vigência da patente da Stratasys, deu para o método. Isso foi feito pra evitar problemas legais, pois o nome “FDM” é registrado.
A lendária e infame patente que impediu que o resto do mundo derretesse plástico em formas tridimensionais por algoritmo computacional foi submetida em 1989 e teve duração de 20 anos. Só esse fato já surpreende muita gente que imaginava ser a impressão 3D uma tecnologia nova. Ou melhor: um conjunto de tecnologias. Há muita técnica diferente que pode ser chamada de Impressão 3D, e o derretimento de plástico nem mesmo foi o primeiro: a primeira técnica foi batizada de estereolitografia e foi patenteada em 1986, por Chuck Hull, o fundador da 3D Systems (em 1981, houve uma patente de método equivalente registrada no Japão que não deu certo e há relatos de peças sendo feitas ainda na década de 70). A estereolitografia também tem um apelido, na forma de abreviação e não sigla: SLA.
Obviamente, há muitas outras técnicas, muitas delas inventadas na década de noventa. Entre elas temos a SLS, ou sinterização seletiva a laser, que com um laser esquenta os grânulos de uma camada de pó até que grudem uns nos outros, e vai adicionando sucessivas camadas e formando sólidos; a SLM, que faz o mesmo, mas com pó de metal; a DLMS, que faz algo parecido não somente esquentando, mas derretendo o metal; a 3DP, que usa camadas de um pó de gesso especial alvejadas por um líquido que ao mesmo tempo colore e endurece; a LOM, Laminated Object Manufacturing, que vai empilhando folhas de papel, pintando e cortando, fazendo uma forma 3D, e daí por diante.
Por que o derretimento de plástico foi a que se popularizou nos tempos de hoje, se nem mesmo foi a primeira? A primeira resposta é a patente, que quando expirou em 2009, e deu ensejo a uma diminuição de preço de duas ordens de grandeza (aproximadamente 100 vezes!) nos preços das impressoras que usam a técnica. A segunda razão também está ligada ao preço: a técnica usa materiais muito facilmente encontráveis na sociedade industrializada de hoje, que são os materiais termoplásticos e com propriedades termoplásticas. Em outras palavras, tornou-se prático e barato prototipar e até mesmo produzir objetos vendáveis com essas máquinas.
Você já deve estar adivinhando aonde eu quero chegar, não? Primeiro, sim, a patente da SLA já caiu e há menos tempo do que se pode esperar. Tudo graças a uma manobra chamada de patent fencing, o registro de patentes relacionadas para “estender” o tempo de vida de uma patente artificialmente. Na prática, a patente da técnica de estereolitografia caiu em 2014 e não 2006. Mesmo antes de 2014, duas empresas se arriscaram a lançar impressoras 3D SLA de baixo custo: a B9 Creator, em 2012, com a impressora 3D de mesmo nome, e a Formlabs, em 2013, com a Form1.
Antes, vamos diferenciar uma coisa: as impressoras usam duas variações diferentes da técnica. Ambas utilizam uma resina líquida fotocurável, o que significa que se determinada luz em intensidade suficiente atinge um ponto na resina, ela sofre reação de polimerização e muda de estado, tornando-se sólida (“curando”). Geralmente, essa luz estará no comprimento de onda ultravioleta A, entre 300 nm e 400 nm, embora existam também as resinas “daylight”, que podem ser curadas com luz visível (acima de 400 nm de comprimento de onda). Cada seção bidimensional do recipiente do líquido endurecida diferencialmente torna-se uma camada daquilo que será a forma tridimensional.
Mesmo essa parte tem variações. Por exemplo, que seção bidimensional do líquido torna-se uma camada? As SLA chamadas de “top-down” (de cima pra baixo, referindo-se à direção do feixe de luz) alvejam a superfície da resina, enquanto que as “bottom-up” (de baixo pra cima, essas mais comuns) alvejam o fundo transparente do tanque de resina. Este último tipo fabrica a peça “de cabeça pra baixo”, pois a plataforma de metal acima do tanque vai “puxando” a peça para cima, enquanto as camadas vão sendo criadas no fundo do líquido.
O método que diferencia a B9 Creator da Form1, no entanto, é como cada camada bidimensional é alvejada por luz. A Form1 usa o método SLA original – tendo até sofrido processo da 3D Systems por violação de patente -, que consiste de um feixe de luz guiado por galvos para percorrer uma trajetória. A B9 Creator, por sua vez, usa um projetor (DLP) de alta resolução, que simplesmente projeta uma imagem de alta intensidade por segundos ou décimos de segundos no fundo do tanque de resina. Ambas a Form1 e B9 Creator são bottom-up.
Até agora, a tecnologia parece bem simples, não? Guiar um laser com galvos não é ciência de foguetes, muito menos subir ou descer uma plataforma ou um tanque (que se faz usando um fuso com castanha). Dividir a peça 3D em camadas é ainda menos complicado que em FDM, precisando de menos ajustes e até de estruturas de suporte mais simples.
Ainda assim, os preços dessas impressoras assustam um pouco. Nos EUA, atualmente as versões mais novas da B9 Creator e da Form2 estão perto dos US$ 4 mil, o que se traduz no Brasil, com os impostos e custos de importação, em quase US$ 30 mil em julho de 2016.
E os materiais? Quanto saem os preços? Resinas fotocuráveis não são algo extremamente raro, mas também não são insumos comuns. Odontologistas usam para próteses. A resina é geralmente vendida por volume, e se estamos acostumados a comprar “um quilo” de filamento, compraremos uma resina em pote de “um litro” ou “meio litro”. E assim como com filamentos de FDM, os preços podem variar bastante: temos desde resinas bem baratas, de US$ 40 o litro, até algumas mais especializadas que custam aproximadamente US$ 200.
Temos algumas bem high-end, cujo preço pode passar de US$ 500, mas são raras. No entanto para chegar ao Brasil, com impostos e frete, não se encontrava litro de resina por menos de US$ 700, com preços mais comuns entre US$ 1 mil e US$ 2 mil. Um detalhe importante é que as impressoras 3D SLA que usam galvos (em vez de DLP) precisam de maior sensibilidade, e as resinas saem um pouco mais caras. Uma resina de SLA pura geralmente funciona em uma SLA/DLP, mas uma de SLA/DLP geralmente dá problemas em SLA pura (considerando que as faixas de frequências de cura sejam as mesmas).
A redenção
Falamos muito até agora sobre a tecnologia, mas, afinal de contas, qual é a mensagem? Se as máquinas e resinas são tão caras, se a tecnologia é tão inacessível, por que dar tanto espaço a ela? Nossas FDMs funcionam muito bem, não? Os plásticos são resistentes, a qualidade é aceitável, os detalhes são perceptíveis.
Exceto, claro, que isso não é verdade. Apesar de FDM funcionar bem para peças grossas e leves, com resistência mecânica adequada para muitos usos, está longe de ser uma tecnologia perfeita. Mesmo a FDM com qualidade mais industrial vai revelar fendas visíveis entre as camadas de plástico. Mesmo a mais rápida delas demorará para imprimir uma peça em resolução maior que 0,1mm, isso se não falhar durante a impressão. Mesmo o material mais aderente vai ter um ponto fraco onde as camadas se unem. Seções finas e verticais ainda são um problema por causa disso, e o gotejamento de plástico em pequenos pontos de certas peças ainda dá um aspecto irregular ao detalhe. Filamentos transparentes e translúcidos, quando impressos, revelam ranhuras que sacrificam a utilidade do plástico para se ver através dele. E como FDM trabalha com derretimento a temperaturas razoavelmente baixas, isso significa que nenhum dos materiais será resistente à temperatura.
Todos esses são problemas que a tecnologia SLA resolve. Alguns modelos chegam a 10µm de altura de camada e 30µm de seção XY do ponto. Seções finas aparecem com perfeição microscópica. As impressões aparecem virtualmente contínuas, com a visibilidade das camadas sendo um acidente evitável – sendo propícia até para objetos realmente translúcidos e transparentes como lentes em resinas “clear”, sem a refração da descontinuidade. Alguns materiais especiais, depois de curados com o laser, resistem no estado sólido a temperaturas altíssimas, impensáveis para um FDM.
Até ao usar a mesma altura de camada de uma impressão FDM típica, 0.1mm, a SLA se sai melhor pela continuidade de detalhes:
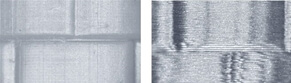
A SLA também não é perfeita, claro. O material-base da maioria das resinas, metil metacrilato, não tem uma pós-cura fácil e não tem grande resistência mecânica, embora ultimamente esse campo esteja melhorando bastante, e materiais com boa dureza (suficiente para aplicações industriais) estejam sendo criados (como a resina “tough”, da Formlabs). E dá para se inferir que devido ao modo como funciona a tecnologia, ela é monocromática por essência. Mexer com resinas é algo que demanda um grande trabalho e proteções, de luvas a óculos, com perigo de toxicidade, e com muitos insumos adicionais – uma cuba onde a impressão é feita é considerada um “artigo descartável” e recomenda-se que seja trocada a cada dois litros de resina.
Mas tudo isso são problemas com solução ou amenizantes. Cubas mais baratas, fundos trocáveis, dutos autolimpantes, resinas super-resistentes, resinas flexíveis, peças encaixáveis.
E o principal: em 2016, poucos anos após a introdução das duas impressoras que se tornaram padrões de fato de mercado – a Open-Source B9 Creator como a DLP e a Form1/2 como SLA, ambas com vários “clones” -, a queda da patente parece ter vingado, e uma democratização vertiginosa da tecnologia já toma lugar. Projetos abertos como o brasileiro openmakerlab e internacionais como a OpenSLA já anunciam projetos de impressoras SLA open source, no estilo reprap; até mesmo uma tradicional companhia, a Autodesk, disponibiliza agora sob licença livre o projeto de uma impressora 3D SLA/DLP inteira, a Ember. E não para por aí, pois até uma resina transparente para ser usada na Ember eles colocaram sob licença open source!
Fabricantes de resinas baratas e resistentes tanto para SLA quanto DLP começam a pipocar e, no Brasil, já temos a MakerTech Labs, que começou a vender litros de resina de alta qualidade por US$ 350 – menos da metade do menor preço até então. Vários dos fabricantes de impressoras 3D nacionais, como a Sethi3D e a Cliever, anunciaram seus modelos de impressora 3D SLA ou SLA/DLP. A B9 Creator ganhou representação oficial no Brasil e outros modelos têm sido bastante importados. Até anúncios de impressoras 3D SLA usadas têm aparecido nos classificados e sites de vendas.
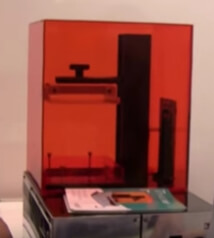
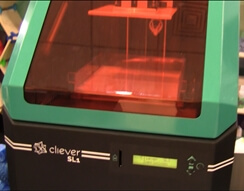
O futuro
Estamos vivenciando o mesmo fenômeno que ocorreu com FDM a partir de 2009. Finalmente, impressoras 3D SLA nacionais apareceram e, dada a ampla documentação da tecnologia e das peças relativamente baratas, o custo das máquinas ainda deve diminuir bastante, assim como os materiais que nos EUA já se encontram equivalentes aos dos filamentos. Não há dúvidas de que com SLA resolvendo muitos dos problemas que assolam FDM, ela será uma tecnologia que compartilhará o espaço e as mentes dos tecnófilos e early adopters, e com o crescimento, o barateamento e a difusão, inevitavelmente se tornará um item tecnológico de massa, como um laptop ou celular, para uso geral – uma fabriquinha portátil que faz a forma que você imaginar.